Welcome to Hardhatengineer.com. I am Varun Patel. In this video, you will learn about the most common questions regarding gasket that you may face during the interview.
You will learn about these questions;
- Can you explain some properties of gasket material?
- What is a centering ring in a spiral wound gasket?
- What are the most common materials used for winding in the Spiral Wound metallic Gasket?
- How to identify the type of winding material in a spiral wound gasket?
- Which type of flanges use of spiral wound gasket is restricted by code?
- What type of gasket is used in Heat Exchanger?
So please watch this video till the end. And don’t forget to subscribe to my channel; that way, you will get regular updates on new videos. You can subscribe right now by just clicking the subscribe button on your screen. So let’s start with the first question.
Can you explain some properties of gasket material?
Gaskets must maintain a seal for an acceptable period against all the operational forces involved. To achieve this, there are eight important properties that any gasket material must possess these properties.
- Impermeability
The gasket should not be porous to the fluid being sealed.
- Compressibility
The gasket should compress into the flange seal imperfections to create the initial seal.
- Stress relaxation (creep resistance)
The gasket should not show significant flow (creep) under the influence of load and temperature. Such flow will allow the bolts to relax, reduce gasket surface stress, and cause leakage.
- Resilience
Although normally stable, flanges move slightly relative to one another under cycling temperature and pressure. The gasket should be capable of compensating for such movements.
- Chemical resistance
The gasket should withstand chemical attack from the process medium being handled. Likewise, the gasket material itself must not contaminate the process medium.
- Temperature resistance
The gasket should be able to withstand the effects of the maximum and minimum temperatures within the process and the external atmospheric temperatures.
- Anti-stick
The gasket has to be easily removable after use.
- Anti-corrosion
The gasket must not cause corrosion of the flange faces.
What is a centering ring in a spiral wound gasket?
To answer this question, you should know the components of the spiral wound gasket. There are three components in the spiral wound gasket.
- Outer Ring
- Winding Material (Filler & Metal Strip)
- Inner Ring/Centering Ring
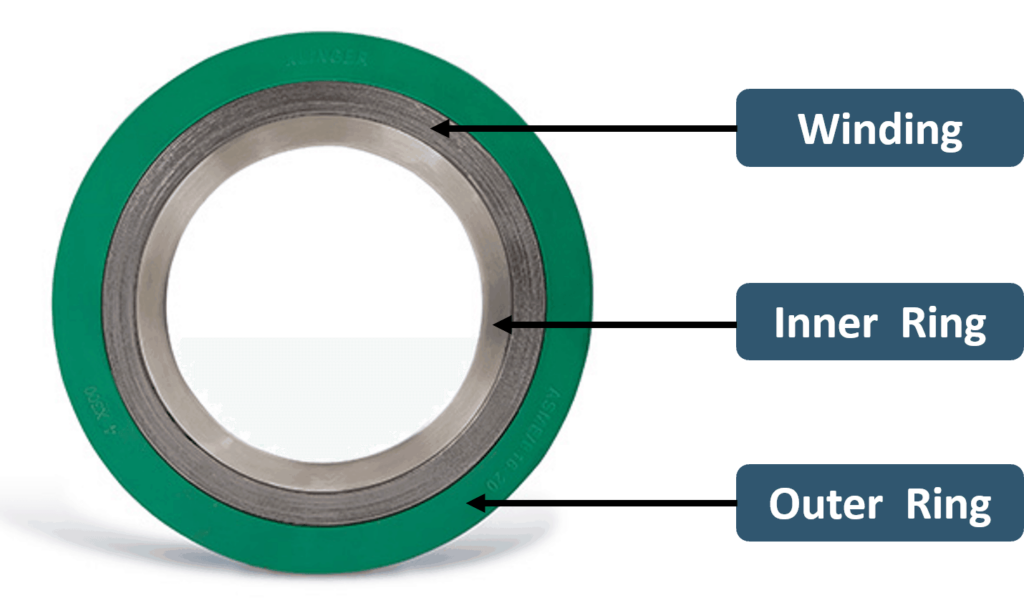
You can see in the image a spiral wound gasket. Many spiral wound gaskets for critical applications include an inner guide ring, also known as a centering ring, which gives the gasket a greater resistance to thermal shock and, in the case of vacuum service, prevents the filler material from being sucked in.
Inner rings should be used with spiral wound gaskets on male-and-female flanges, such as those found in heat-exchanger, shell, channel, and cover-flange joints.
Gasket Quiz – Test yourself, Take This Quiz
Unlock New Skills with Our Best Selling Online Courses
What are the most common materials used for winding and filler in the Spiral Wound metallic Gasket?
Winding material is a thin metal strip that is used to hold the filler material. Stainless steel grades 304, 316, and 321 are popular material grades for winding. The selection of the filler material is made based on the fluid service. Graphite, PTFE, and ceramic material are well-known filler materials used with a spiral wound gasket.
How to identify the type of winding material in a spiral wound gasket?
- For easy identification, Spiral Wound Gaskets are painted in accordance with ASME B16.20.
- The solid color on the EDGE of the outer ring indicates the metallic winding material.
- The striped color on the edge indicates the non-metallic filler used between the metal winding.
- The color on the outer ring’s surface indicates the outer ring’s material.
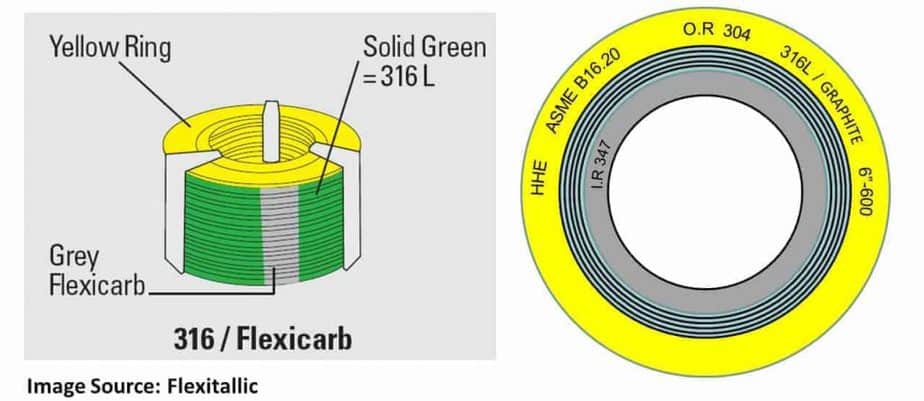
This image shows the sample marking of 6” 300 Class Spiral wound gaskets, manufactured in accordance with ASME B16.20. Here, the outer ring is of SS304, the winding material is SS316L metal strip, and the filler material is flexible graphite.
Which type of flanges use of spiral wound gasket is restricted by code?
ASME B 16.5 does not recommend the use of spiral wound gaskets on 150# rating flanges other than welding neck and lapped joint type.
What type of gasket is used in Heat Exchanger?
Metal jacketed gaskets are commonly used in heat exchangers. In Metal Jacketed Gasket, Soft filler material is enclosed in a thin sheet of a metal jacket. You can see the image of the channel cover gasket.
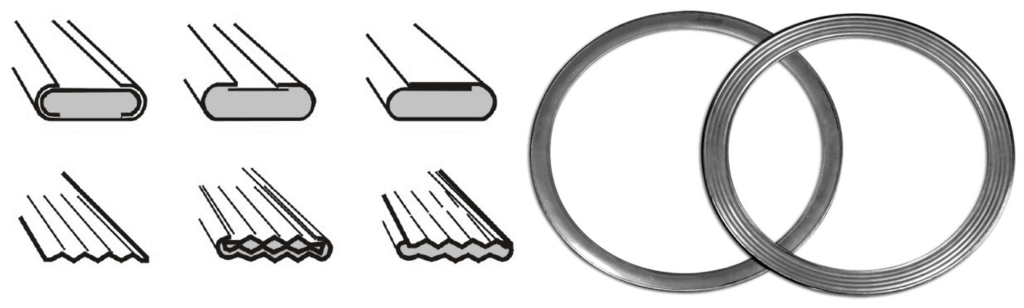
This is the end of the video. I hope that you have learned from this video. In the next video, I will explain to you a few more important questions related to piping components. So keep on checking my youtube channel for new videos.
Visit my website hardhatengineer.com for free study materials, and don’t forget to subscribe to my channel to get regular updates on new videos. Please like and share my video with your friends. If you want to request a video, please write in the comment. See you soon; goodbye, take care.
Are You Piping Components Master?