A pinch valve is a type of valve used for flow control in various industries, particularly in applications involving slurry. It operates by pinching a flexible rubber sleeve to control the flow of fluid or solid through the valve. These valves are widely used in industries such as mining, wastewater treatment, and chemical processing industries.
It is also known as a clamp valve. It is a linear motion valve used to start, regulate, and stop the flow of fluid. It uses a rubber tube, also known as a pinch tube, and a pinch mechanism to control the fluid. This valve is the simplest in any valve design.
Table of Contents
Overview
Pinch valves are unique in their design and function. They consist of a valve body, an actuator, and a flexible rubber sleeve, also known as the pinch tube. The valve body holds the rubber sleeve that creates a flow path for the fluid or slurry to pass through, while the actuator is responsible for operating the pinch valve. The rubber sleeve acts as the gate that regulates the flow by pinching or releasing the sleeve.
See the image below.
Image Source – Red Valve
Pinch valves offer several advantages over other types of valves in slurry medium. They provide a full bore opening, which eliminates any obstruction in the flow path. This feature makes them ideal for handling slurry or fluids containing solid particles. It provides excellent flow control capabilities due to the elastomer sleeve.
Unlock New Skills with Our Best Selling Online Courses
How Pinch Valves Work?
The operation of a pinch valve is quite simple. When the actuator is triggered, it applies pressure to the rubber sleeve, causing it to deform and pinch off the flow path. This creates a tight seal and completely stops the flow. When the actuator is released, the pressure is relieved, and the rubber sleeve returns to its original shape, allowing the flow to resume. As you can see in the image below.
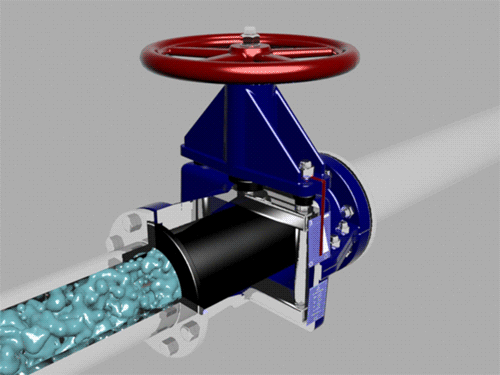
Image Source – Pinch Valve (bpaspb.ru)
Piping Component Quiz – Test yourself, Take This Quiz
Types of Pinch Valve
There are several types of pinch valves available for various applications, depending on their operating mechanism:
- Air Operated Pinch Valves (Pneumatic Pinch)
- Solenoid Pinch Valves
- Mechanical Pinch Valves
Each type has its own advantages and is suitable for different operating conditions.
Air actuated pinch valves are controlled by a pneumatic actuator and offer precise control over the flow. They are commonly used in industries that require accurate flow regulation, such as the food and pharmaceutical industries.
Solenoid pinch valves, on the other hand, use an electromagnetic solenoid to operate the valve. They are often used in applications where fast and reliable response times are critical.
Mechanical pinch valves, as the name suggests, operate mechanically without the need for external control. They are suitable for low-pressure applications and provide a cost-effective solution. Mechanical pinch valves are often used in industries where simplicity and reliability are prioritized.
How to Select the Best Pinch Valve for Application
When selecting a pinch valve for a specific application, several factors should be taken into consideration. These factors include the pressure rating, temperature range, flow requirement, actuation method, maintenance and service life, and the materials used in the valve construction.
Pressure Rating
You have to determine the maximum pressure the valve will be exposed to during operation and accordingly choose a pinch valve with a pressure rating to ensure the safety and reliability of the system.
Temperature Range
Consider the temperature range of your application, pinch valves should be selected based on their ability to withstand the temperatures encountered in the process.
Flow Requirements
Pinch valves come in various sizes and the diameter of the tubing or sleeve that will impact the flow capacity. Evaluate the flow rate and capacity needed for your application and select the valve accordingly.
Actuation Method
Pinch valves can be actuated manually, pneumatically, or electrically. Choose the method that best suits your application and process requirements. If automation is required, consider the air actuation or solenoid method.
Maintenance and Service Life Cycle
Maintenance and cycle life are important considerations when selecting a pinch valve. It is crucial to choose a valve that requires minimal maintenance and has a long service life cycle. This ensures that the valve will operate reliably and provide uninterrupted service for an extended period.
Materials
The materials used in the construction of the valve body and rubber sleeve are crucial for compatibility with the fluid or slurry being handled. Different materials offer varying levels of resistance to abrasion, corrosion, and chemical attack.
It is important to select a pinch valve with materials that are suitable for the specific application to ensure durability and long-lasting performance. Sleeve material available for pinch tubes can be Natural Rubber, Neoprene, EPDM (Ethylene Propylene Diene Monomer), Nitrile, Hypalon, or Viton.
Valve Quiz – Test yourself, Take This Quiz
Applications of Pinch Valves
Pinch valves find applications in various industries due to their unique design and capabilities. They are commonly used in industries such as mining, wastewater treatment, chemical processing, food and beverage, and many more. Some specific industrial applications of pinch valves include:
- Slurry transportation and handling
- Control of abrasive or corrosive fluids
- Powder handling and processing
- Flow control in wet and dry applications
- Handling of viscous fluids
Advantages of Pinch Valves
Pinch valves offer several advantages over other types of valves in certain applications. One of the main advantages is their ability to handle abrasive or corrosive materials. The rubber sleeve acts as a barrier between the fluid and the valve body, preventing direct contact and minimizing the risk of corrosion or contamination.
Another advantage of pinch valves is their wide range of applications. They can handle a variety of fluids, including slurries, powders, and even gaseous substances. This versatility makes pinch valves suitable for use in industries such as mining, chemical processing, wastewater treatment, and many more.
In addition, pinch valves are known for their simple design and ease of maintenance. The rubber sleeve can be easily replaced when it wears out or gets damaged, without the need for complex disassembly or reassembly. This reduces downtime and allows for easy and cost-effective maintenance.
Unlock New Skills with Our Best Selling Online Courses
Disadvantages of Pinch Valves
While pinch valves offer numerous advantages, they also have some drawbacks that should be considered. One limitation of pinch valves is their relatively low pressure rating. They are typically suitable for low to medium pressure applications and may not be suitable for high-pressure industries.
Another disadvantage is the potential for wear and tear on the rubber/elastomer sleeve. Depending on the material being handled, the rubber sleeve may degrade over time, requiring regular replacement. However, this is a minor drawback considering the ease of replacing the sleeve compared to other types of valves that may require more extensive maintenance.
Conclusion
Pinch valves are versatile flow control valves that find extensive use in industries handling slurries and abrasive materials. Their unique design and capabilities make them a popular choice for applications requiring precise flow control. By understanding the advantages, disadvantages, and selection criteria of pinch valves, you can make informed decisions to ensure optimal performance and efficiency in their operations.
Click here to learn about Other Types of Valve.
Unlock New Skills with Our Best Selling Online Courses