Material traceability is extremely important during fabrication of piping and equipment that will be used in Oil and Gas facilities. In this article, you will learn about the importance of material traceability during fabrication.
You will learn what material traceability is, why it is important, and how traceability is maintained throughout the fabrication.
What is Material Traceability?
Material traceability refers to the process of tracing back all the bulk materials used in fabrication, such as pipes, fittings, flanges, and plates, to their origin at any given time.
It involves establishing a system that can trace each material along with its original material test certificate. This system allows you to identify the supplier, the specific material, and its associated information, like the heat number, whenever required.
Why is Material Traceability Important?
Material traceability plays a crucial role in ensuring the integrity and reliability of fabricated piping and equipment, especially in industries like Oil and Gas. Let’s understand why it holds such significance.
Identification of Defective Materials
In the fabrication process, there may be instances where certain materials turn out to be faulty or fail to meet the required standards. Identifying such defective materials becomes essential to avoid potential failures during operation.
In one of the projects that I worked on, we got a few 100 flanges from one supplier. After a few months, we got a letter from the supplier that there was an issue with one particular lot. These flanges were failing in the impact test.
Now that most of the fabrication work was already completed, how will you identify those flanges with problems?
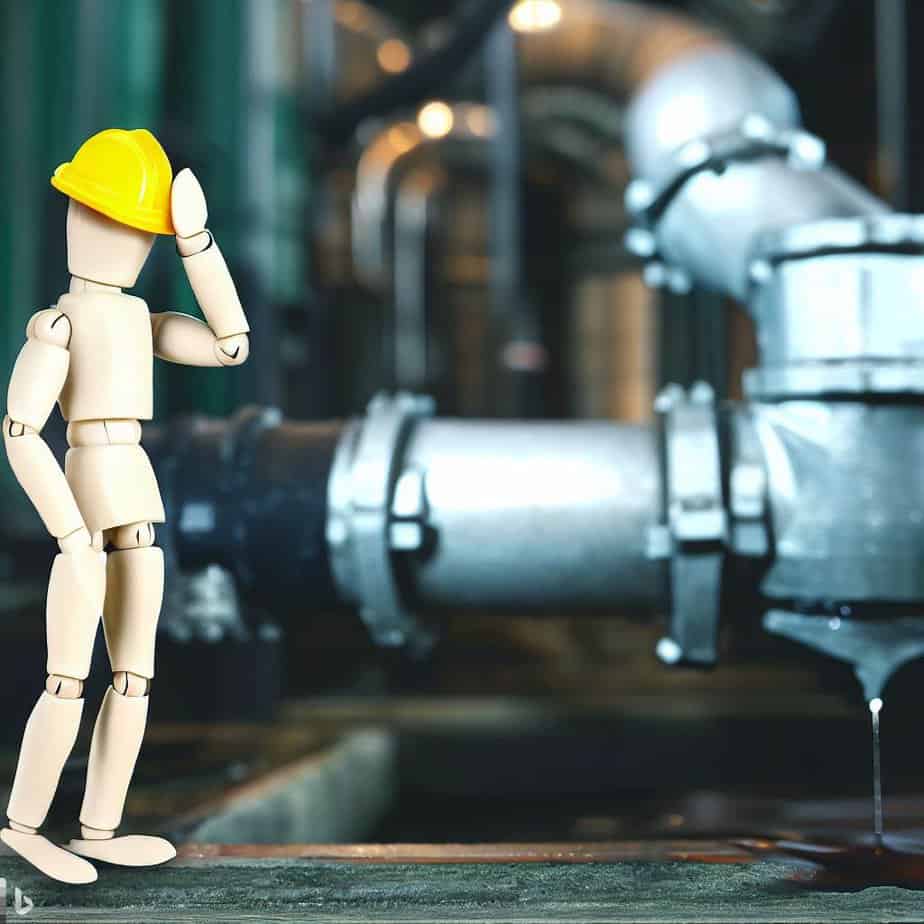
Material traceability enables you to trace and replace these faulty materials promptly, ensuring the safety and efficiency of the process plant.
A similar issue may arise during the operation. Let’s say some materials fail within a short operation time due to metallurgical or heat treatment-related issues. To avoid future failure at other places, you must trace all such defective materials and replace them as soon as possible.
In all such situations, you must replace faulty materials to safeguard your process plant. With the help of a material traceability system in your fabrication, you can easily trace and replace such materials.
Piping Component Quiz – Test yourself, Take This Quiz
Compliance with Quality Standards
Material traceability is closely linked to quality assurance and compliance. By maintaining a traceability system, you can demonstrate adherence to quality standards, regulatory requirements, and industry-specific certifications. This not only enhances your credibility but also provides assurance to stakeholders regarding the quality of the fabricated products.
Efficient Maintenance and Repair
During the operation of a process plant, maintenance and repair activities are inevitable. Material traceability simplifies these tasks by enabling easy identification and replacement of specific components or materials. It saves time and resources that would otherwise be spent on extensive inspections or trial-and-error approaches.
How to Maintain Material Traceability?
Now that we understand the significance of material traceability, let’s learn how it is maintained during fabrication.
Inward Material Inspection
The process begins with an inward material inspection, which verifies the quality and conformity of incoming materials. This inspection ensures that the materials meet the required specifications before they are used in the fabrication. You can learn more about this process in my earlier video given below.
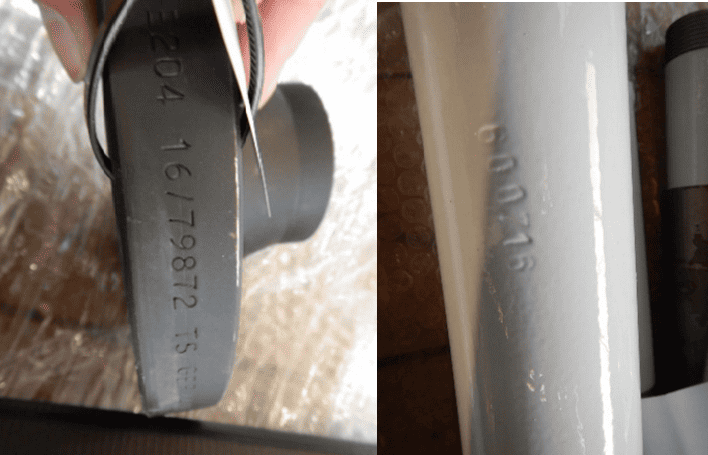
Marking and Material Identification
Before using materials like pipes and plates for fabrication, they are marked with part numbers and Material IDs. These markings serve as a unique identifier for each component and help maintain traceability.
An inspection engineer checks the marking and puts a unique stamp on each part, ensuring their traceability even if the original manufacturer’s marking is no longer visible. Markings can be made using a hard punch or a paint marker, depending on the thickness of the material.
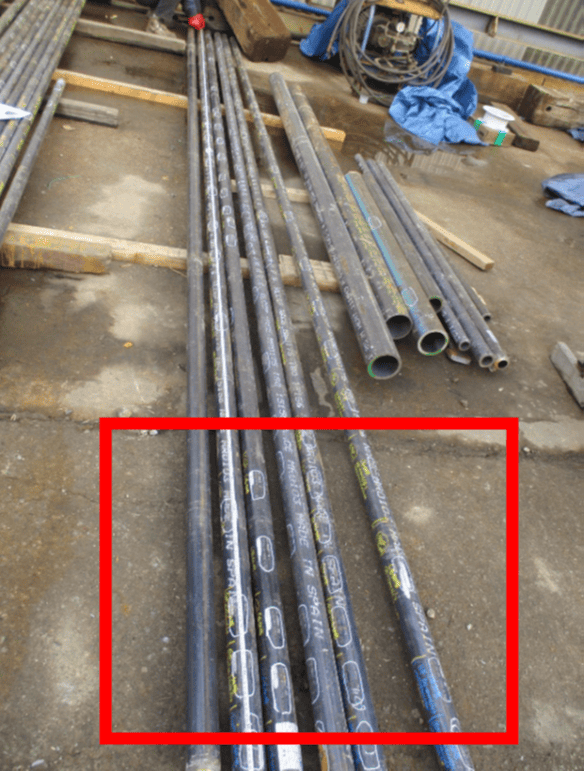
Fit-up Inspection
During the fit-up stage, components like fittings, flanges, and pipes are assembled for welding. Each component is marked individually, and their markings are recorded during a fit-up inspection. The heat numbers of these components are also documented. This information is crucial for material traceability and gets transferred to the line history steel when prepared.
During Fabrication
Now, let’s learn how to ensure proper traceability in the next stages of fabrication.
Here, in the image, you can see a pipe spool fitup. There are three components and two welding joints in this spool. A flange, pipe, and elbow.
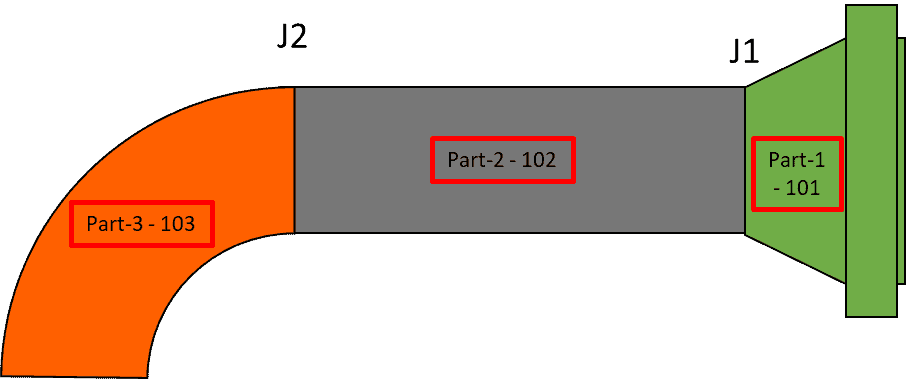
Now we have three components that are going to weld together. Once these are welded, they are a permanent part of the project. So, if we establish tracking at this stage, it will remain traceable forever.
Part No. | Part Description |
---|---|
Part-1 – 101 | Flange – 6”, Class 150, A105 Gr.B Sch80 |
Part-2 – 102 | Pipe – 6” Sch 80, A106 Gr.B |
Part-3 – 103 | 90° Elbow – 6” Sch 80 – A234 WPB |
Below, you can see the sample fitup inspection report. This report records things like drawings, lines, spool, joint number, and the joint’s dimension.
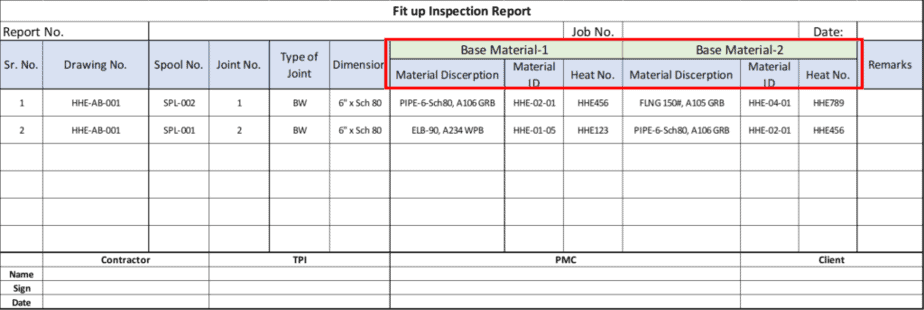
Now, these two columns are of interest and critical for material traceability. In our example, joint number two is elbow to pipe. So, the first column records base material part one, a 90-degree elbow, and the second part, a pipe.
Similarly, the first joint is a pipe to flange. You have to record the material details of both components. When the line history steel is prepared, these material details will get transferred into that. So this is how material traceability is maintained in the piping.
Metal Tagging and Spool Numbering
To ensure traceability throughout the fabrication and installation process, it is common practice to put metal tags on spools or write the spool numbers inside the pipes using a paint marker. This allows for easy identification and tracking of specific spools or welded materials, even after painting and during field installation.
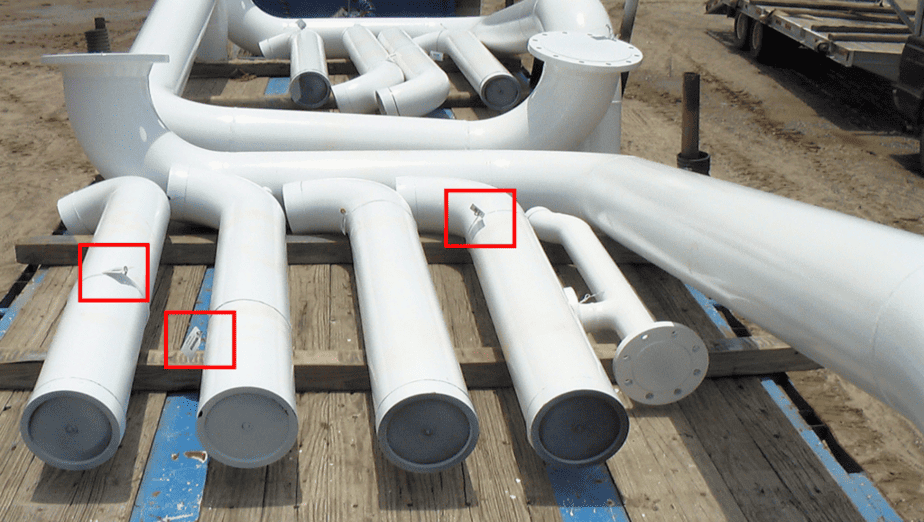
Image Source – https://www.kjservices.com/
Are You Piping Components Master?
Conclusion
Material traceability is of utmost importance during the fabrication of piping and equipment in industries like Oil and Gas. It ensures the identification of defective materials and compliance with quality standards and facilitates efficient maintenance and repair activities.
By establishing a robust material traceability system, you can enhance the reliability and safety of your process plant.