In this article, I will explain to you the flange isolation joint and gasket kit that is used to achieve this objective. I will explain to you about
- What is the Flange Isolation Joint?
- Why and where it is used
- Components of Isolation Joint
- Proper installation of flange Isolation Joint.
I am thankful to GPT industries for allowing me to use their proprietary material in this video.
What is the flange isolation joint?
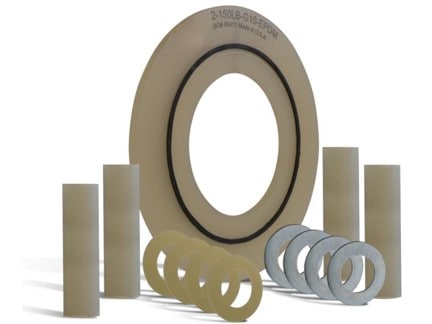
Well, don’t get confused by the name. It is not blinding of a flange that stops the fluid. This is a different kind of isolation. It is going to isolate the current. Current in pipe flange? Yes, you heard it right.
A flange isolation gasket kit is used to protect pipeline flanges from corrosion that happens due to galvanic corrosion. I will explain to you how this corrosion works in the pipeline in more detail in a minute. Here you can see in the photo that it is a specially designed gasket kit that involves a gasket, nonmetallic sleeves for stud, and nonmetallic washers.
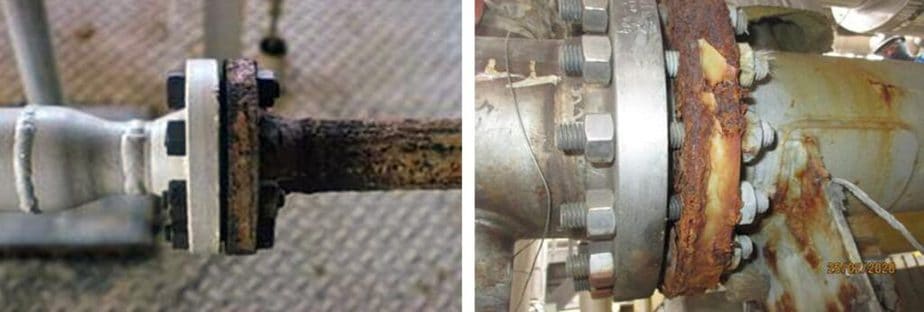
The first place you can see the use of a gasket kit is when dissimilar metal joints are involved. For example, you can see that one side flange is made of carbon steel, and the other is of stainless steel. You can see that the carbon steel flange is badly corroded in both these photos as no isolation gasket is used.
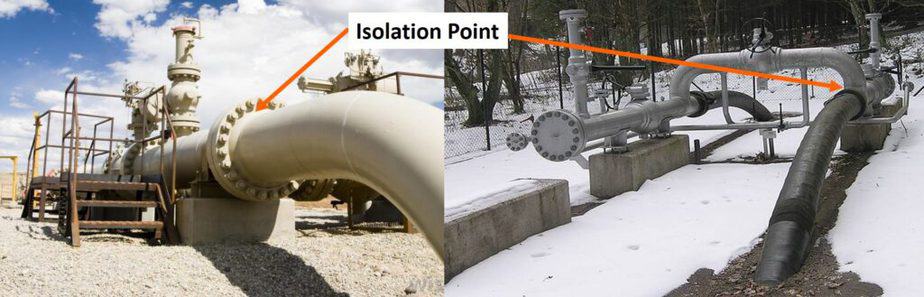
P&ID Quiz – Test yourself, Take This Quiz
Unlock New Skills with Our Best Selling Online Courses
The second place where you can see this flange isolation gasket kit is when the pipeline change from above ground to underground or another way around. Usually, the underground pipeline is protected by cathodic protection.
To prevent current leakage to the aboveground pipeline, you have to use either an isolation joint or an isolation gasket kit. By doing this, you can save electricity and prevent the damage of aboveground piping paint.
Now, you know why and where the flange isolation gasket kit is used. Let’s learn how pipe flange protection is achieved using this kit.
How does Galvanic Corrosion work?
As explained to you earlier, the main reason behind the corroded flange is galvanic corrosion.
Here, you can see that stainless steel and carbon steel flanges are joined without an isolation gasket. This happens as both these materials are having a different value of galvanic voltage.
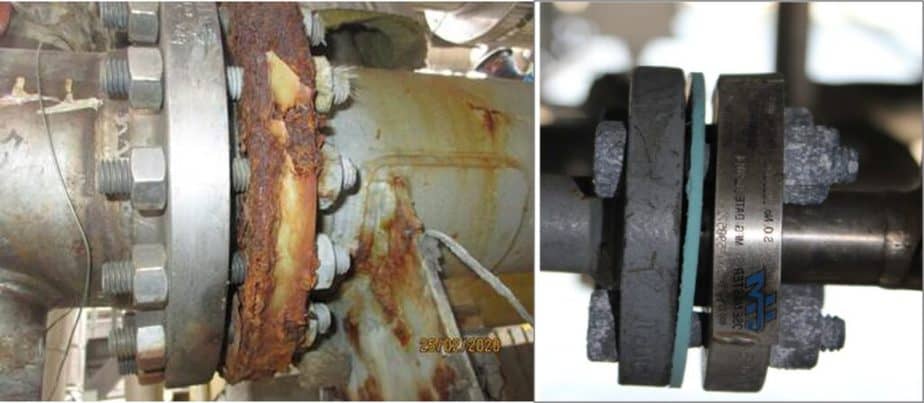
This chart shows the various commonly used materials and galvanic values corresponding to the same. Materials at the top of the chart are more noble materials than materials at the bottom of the chart. What does it mean?
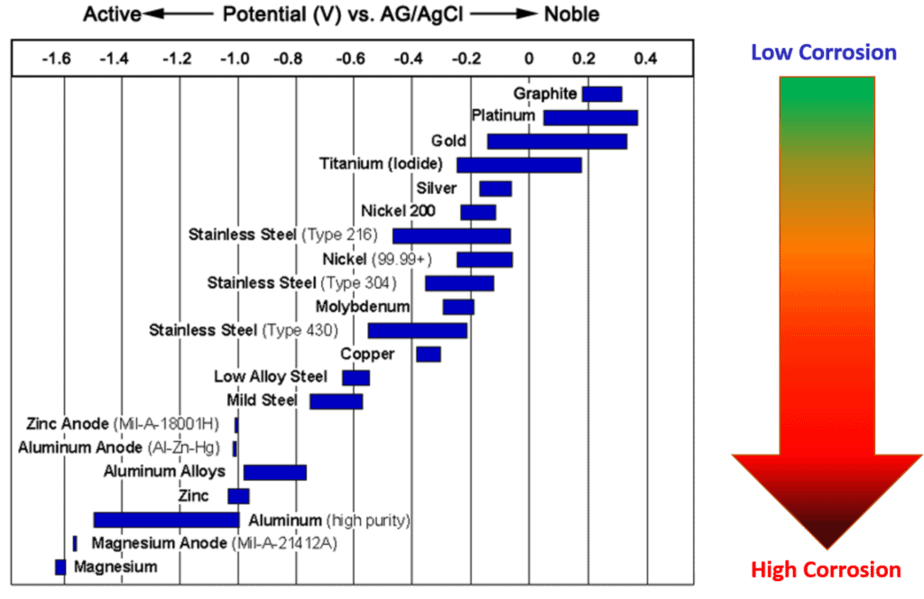
Materials such as gold and silver don’t corrode easily, whereas materials such as zinc and carbon steel corrode easily in a corrosive environment. Now, from this chart, you can see that stainless steel is nobler than carbon steel.
So, when these two materials are connected, the rate of corrosion will accelerate as CS will behave as an anode, and SS will behave like a cathode.
Four elements of Galvanic Corrosion.
To start corrosion, you must need four things to present at the same time.
- Anode
- Cathode
- Metallic path
- Electrolyte
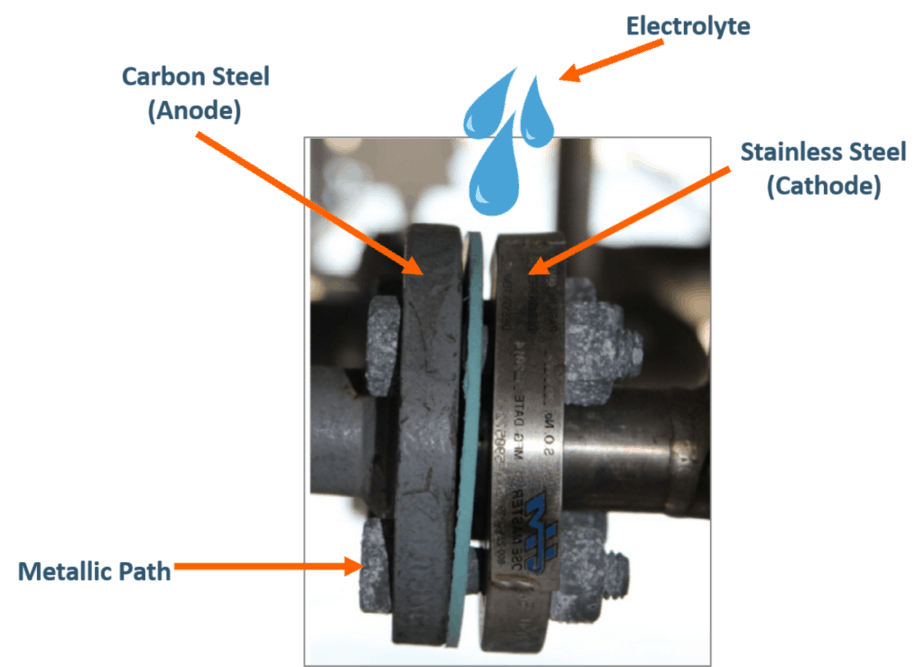
So, in the ideal condition, we have three things present in any flange connection: Anode, cathode, and metallic path through studs. If your flange connection is free from the electrolyte, you don’t need any protection.
But in real life, you have rain, water, moisture, sand, and many more things that work as an electrolyte. So, flange protection is required. Like the fire triangle, you can stop the process if you remove any one element.
Here, you cannot remove anode or cathode, and removing the presence of electrolyte is impossible. So, the only option left is to remove the metallic path. And the flange isolation gasket kit does the same. It stops the flow of the electron from cathode to anode.
Components of Isolation Gasket Kit
- Specially design Gasket
- Nonmetallic sleeves
- Nonmetallic washers
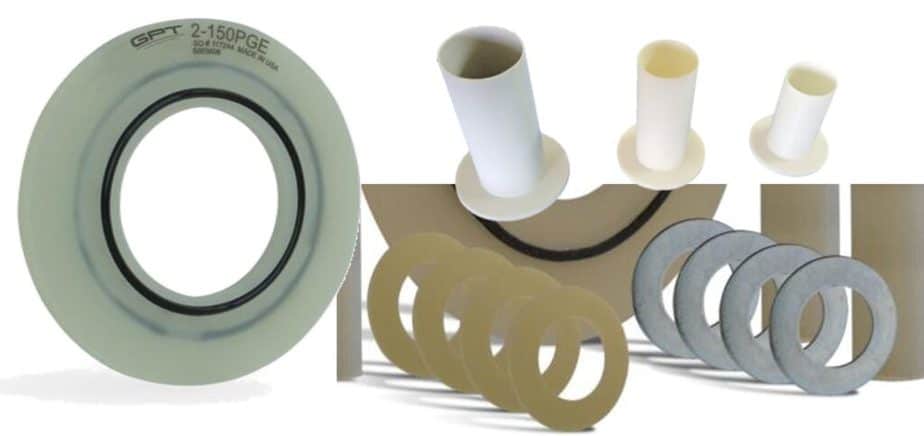
The isolation gasket kit includes a specially designed non-conductive gasket that provides necessary sealing.
Stud sleeves are used to prevent any metal-to-metal contact between stud and flange. It is made of tough nonmetallic material to handle some degree of abuse while the flange joint is tightened.
The next component of the kit is a washer. A nonmetallic washer prevents nuts from contacting the flange. That is how you completely disconnect both cs and ss flanges. In cathodic protection, the isolation gasket kit works the same way and prevents current passing from underground to the aboveground pipeline.
Good Practice for Flange Isolation Gasket
There are a few good practices to achieve the full benefit of flange isolation using this special kit.
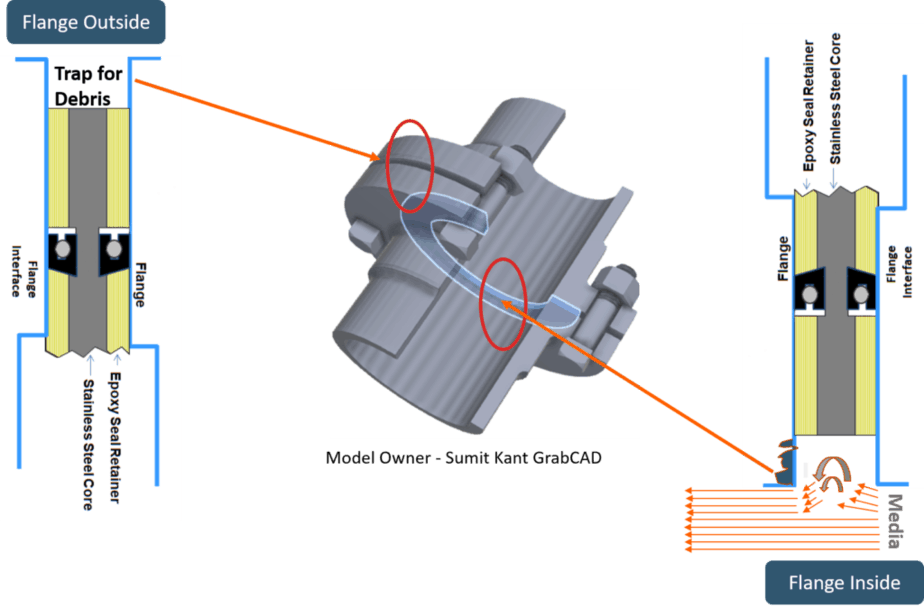
The gap between the two flanges should be avoided in the case of the dissimilar joint. If there is a gap outside of the flange joint, there is a chance of water or dust accumulation. This will work as a path that will lead to corrosion. Similarly, it would be best if you also matched the gasket at the pipe ID. If the gasket ID is more than the pipe, it will create a vortex in the fluid. This is also an undesirable condition, so you have to match ID.
Images Source – GPT Industries
Are You Piping Components Master?