Ball valves are some of the most commonly used valves in industrial equipment and systems to manage fluid flow. Depending upon the systems and applications, many industrial setups need bubble-tight systems that are successfully achieved using ball valves, particularly for chemical processing applications.
In this article, we’ll explain the following:
- What is a bubble-tight valve?
- Need for bubble-tight systems
- Mechanism and parts of ball valves
- How do ball valves achieve ball-tight shutoff
- Advantages of using a ball valve
To learn about 6 Types of Ball Valve – Floating, Trunnion Mounted & more, visit this article.
What is a bubble-tight valve?
It’s a phrase describing the sealing ability of a valve. During pressure testing of a new valve in the closed position, leakage past the seats is collected and bubbled through water. No bubbles should be observed in a prescribed time to qualify as bubble-tight.
The ANSI VI leakage rating test is done with air or nitrogen, but there are also instances where helium or a mixture of helium and nitrogen is used.
ANSI Leakage Classification
Though there exist several ANSI seat leakage classifications, industrial application requirements frequently involve one of the following leakages classes:
- Class III
- Class IV
- Class VI.
They define the permissible leakage rates through a given valve’s seats when subjected to specific test mediums under specific test pressures.
- ANSI Class III valves have a maximum allowable leakage rate of 0.1% of the rated capacity of the valve.
- ANSI Class IV valves have a maximum allowable leakage rate of 0.01% of the rated capacity of the valve.
- ANSI Class VI valves are often called “bubble tight shut-off”. However, they also have a specific permissible leakage rate defined in bubbles per minute or in mL per minute. The leakage from Class VI ball valves should not exceed 0.15-6.75 mL per minute for valves whose diameters range between 1 and 8 inches.
The value of the allowed frequency of bubbles per minute or volume of mL per minute depends on the nominal port diameter of the valve itself. In other words, a 2” valve is permitted fewer bubbles per minute in leakage than a 6” valve would be permitted to obtain a Class VI rating.
ANSI Class III and ANSI Class IV typically apply to hard seated valves, while ANSI class VI typically applies to soft seated valves.
Valve Quiz – Test yourself, Take This Quiz
Need for bubble-tight systems
Numerous industries have found applications for bubble-tight systems. From industrial processes to public water pipelines, bubble-tight systems are necessary for many.
Some common applications include:
- Chemical processing
- Oil and gas
- Cryogenics
- Water filtration plants
The ball valve’s mechanism offers great sealing capabilities with little to no leakage. Due to their versatility and performance throughout various industries, ball valves are a regular go-to solution for bubble-tight shut-off applications.
Mechanism of a Ball Valve
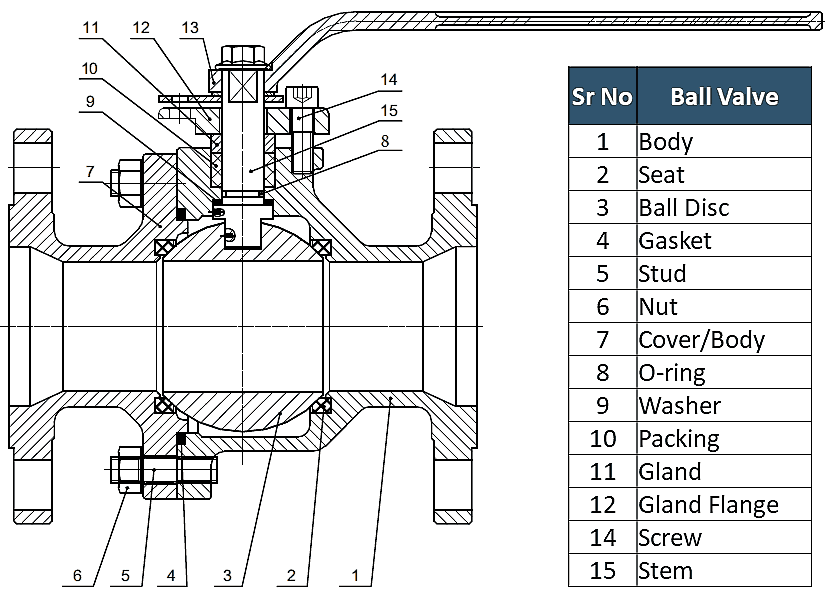
A ball valve has a solid forged metal ball acting as a barrier. When the operator turns the valve handle to the open or valve ‘ON’ position, the ball allows passage of the fluid. The ball obstructs the flow in the closed condition or valve ‘OFF’ condition.
In essence, the ball turns 90 degrees by means of the actuator or lever to control the fluid through pipes. Typically, companies manufacture these valves to fully stroke through a 90 degree, or quarter-turn, rotation, but sometimes a valve that operates through a rotation greater than 90 degrees, perhaps 180 degrees or even 270 degrees, proves necessary.
Therefore, when the valve is in the open position, the lever is positioned parallel to the direction of the flow. When the flow has to be stopped, the operator or actuator turns the lever and strokes the valve back to its original position, thus closing the valve and returning the lever to a position perpendicular to the fluid flow.
There are three types of ball valves based on the fixture of the ball:
- In a floating ball valve, the ball is suspended on the stem and partially relies on the internal pressure of the fluid. When the valve is closed, upstream pressure pushes the ball into a cupped grove of the same size located downstream. The closure ensures the sealing of the opening and blocks the flow.
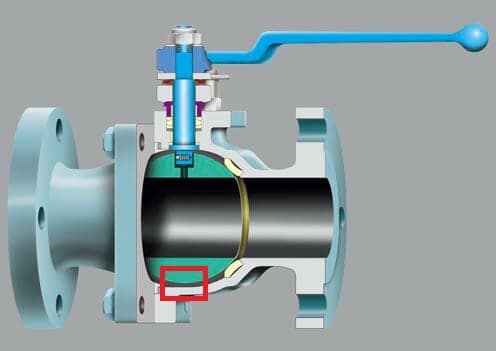
- In the case of a trunnion-mounted ball valve, the ball is supported by a trunnion at the bottom of the ball to keep it stationary. These trunnions absorb fluid pressure and balance it off in closed conditions to reduce friction. Spring-loaded seats push against the ball so that only rotary motion about its axis is possible. In closed conditions, the spring force holding the seats against the ball ensures a tight seal against the service media.
- Rising stem ball valves operate on the tilt-and-turn mechanism. The ball gets fixed on the seat in closed condition to seal fluid and airflow. The ball is tilted in an open position due to fluid force, creating a passage for fluid media.
Based on the mechanism, ball valves offer very good control of fluids, regulate pressurized gases, and can be used for a moderate level of throttling services.
Ball Valves and Sealing Action
Depending on the actuation method, ball valves are generally a fast-acting quarter-turn device. They have a ported ball or sphere which moves through 90O to block or initiate the flow of fluids. The sealing efficiency of the ball valves depends on the design of the seat, choice of sealing material, packing and the configuration of port(s). Therefore, ball valves are critical for pipelines that require quick shut-off.
Ball valves used for isolating fluid pipelines often have O-ring packing styles. These valves are common in low-cycle fluid applications and are designed following API 6D standards. They contain seal injection ports that enhance their bubble-tight sealing capabilities.
General service ball valves are vital for isolation and controlling fluid flow in diverse applications. They are designed following API 6D specifications. These valves have mechanically retained seals. The seals provide a bubble-tight shut-off and can withstand extreme fluid conditions during throttling.
Severe service ball valves are designed to withstand cavitation while providing excellent sealing. These ball valves are engineered with anti-cavitation trims that accommodate extreme pressure drops across the valves. The anti-cavitation trim ensures the valve can withstand extreme fluid flow conditions without losing its bubble-tight sealing characteristics.
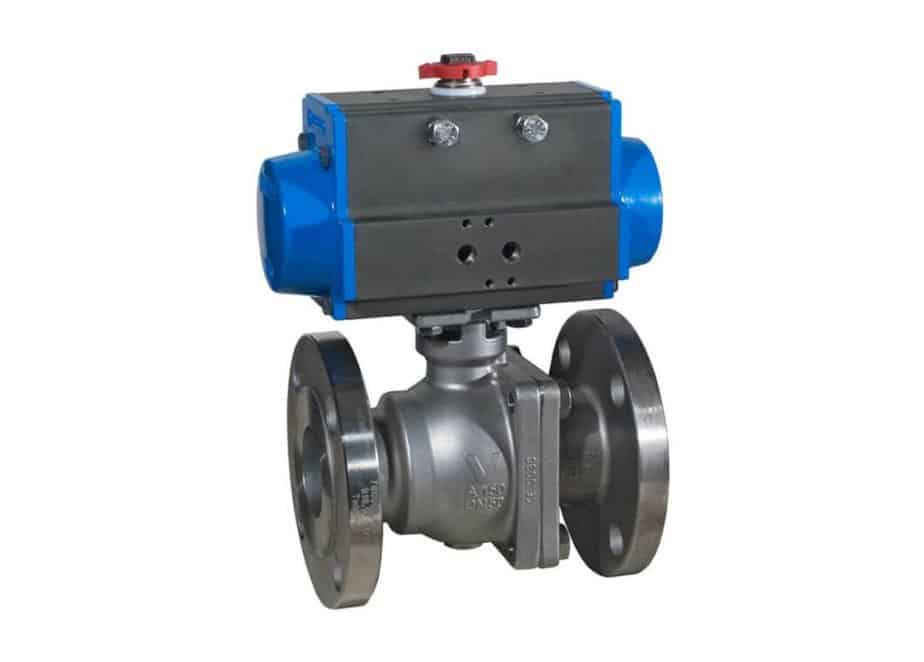
Image Source: https://valveman.com/products/bonomi-8p766000/
How do ball valves achieve bubble-tight shut-off?
A bubble-tight system is achieved using a ball and a seat that is made of either metal or thermoplastics.
Metal-seated Ball Valves:
Metals have higher resistance to temperature and wear and tear. Hence, this type of ball valve can be exposed up to temperatures of 1000º F and is ideal for corrosive applications. These metals can be further hardened by using appropriate processes like spraying or hard-facing using tungsten carbide.
The sealing surfaces of the metal seated valve undergo a finishing process called lapping. They are machined to a smooth finish using a suitable abrasive to ensure tight contact between the sealing surfaces.
Metal-seated ball valves withstand extreme process temperatures and pressure. These valves are critical for different industrial applications that experience massive changes in fluid flow conditions. Temperature variations associated with heating can cause expansion of the valve trim.
In other cases, severe temperature drops can cause contraction, which may deform internal valve components. Requiring a valve capable of reliable shut-off performance despite facing these extremes remains a critical reason that many applications necessitate the selection of such metal-seated ball valves.
These valves are also found in corrosive fluid service. The metal seat can withstand several cycles controlling the flow of chemicals, acids and abrasive fluids. One leading cause of valve leakage is the erosion-corrosion of the seat, seals and internal valve components. When the valve seat comes into contact with the service fluids, it resists corrosion due to abrasion and corrosion. It provides a tight seal to facilitate long-term fluid service.
The excellent sealing characteristics of metal-seated ball valves make them suitable for pipelines conveying combustible fluids. They are also utilized in fire suppression systems and chemical processing plants.
Such valves enhance operational safety since they do not permit minute fluid leakages. They accommodate excessive stress due to fluid pressure and viscous fluids, thereby increasing the efficiency and safety of piping systems in different facilities.
Soft-seat Valves:
Soft seats are usually made of thermoplastics and are excellent when the fluid is chemically reactive. However, these have limitations when using abrasive or hard, dirty fluid. This type of valve is cost-effective in comparison with metal-seated valves.
Soft-seated valves are widespread in bubble-tight fluid applications due to their excellent sealing characteristics and chemical compatibility. Soft-seated valves exhibit superb sealing characteristics in low and medium-pressure processes and fluid applications operating at temperatures below 500oF.
Soft-seated valves are critical for Class VI shut-off applications and provide sufficient sealing against leakages and fugitive emissions in chemical processing pipelines.
The base material for manufacturing soft valve seals is often reinforced using different compounds to improve their performance in diverse fluid applications. They can be backed using glass, graphite or fiber. These seats have unique designs that determine the allowable process temperature and pressure.
Advantages of Ball Valves
Apart from a tight sealing of pipes, ball valves also offer:
- The possibility of visual detection for the open or close position of a manual valve. This can be determined by observing the position of the handle,
- High flow capacity with lower pressure drops and lower head losses,
- Lower possibilities of leakage,
- Improved control of fluid flow,
- Higher durability and relatively lower wear over years of operation.
Conclusion
Achieving bubble tight systems can be difficult, but the mechanism and body of ball valves offer exceptional shut-off characteristics and meet the desired flow pressure and temperature requirements.
These characteristics of ball valves make them a great and popular choice in achieving bubble-tight systems and a more effective, and thus valuable, selection than other economical alternatives.
Are You Piping Components Master?