Spiral wound gaskets and kammprofile gaskets are both widely used in industrial sealing applications. Let’s see some of the key differences between them.
Here in the table, you can see a detailed comparison between these two types of gaskets.
Feature | Spiral Wound Gasket | Kammprofile Gasket |
---|---|---|
Construction | Made of alternating layers of metal and soft filler (e.g., graphite, PTFE) wound into a spiral shape. | A solid metal core with a machined profile (grooves) on both sides, often coated with a sealing material. |
Sealing Mechanism | Relies on the compression of metal and filler layers to create a seal. | Utilizes the grooves to hold the sealing material, which deforms under pressure to create a seal. |
Material Flexibility | Can accommodate thermal cycling and pressure fluctuations due to its flexibility. | More rigid but provides excellent sealing at high pressures and temperatures. |
Best Use Cases | Ideal for flange joints in piping systems, heat exchangers, and vessels where flexibility is needed. | Suitable for applications requiring high integrity seals, such as critical flanges, heat exchangers, and high-pressure systems. |
Pressure and Temperature | Performs well in high-pressure and high-temperature applications but is less robust than kammprofile in extreme cases. | Better for very high-pressure and high-temperature applications due to its solid metal core. |
Reusability | Generally single-use, especially when damaged during disassembly. | Can be reused after cleaning and re-coating the sealing material, provided the core remains undamaged. |
Thickness Tolerance | Thickness varies slightly due to the layering process. | Offers more consistent thickness due to its solid core design. |
Installation Sensitivity | Requires careful centering and controlled bolt tightening to avoid damage to the filler material. | Easier to install and less sensitive to uneven bolt loads. |
Cost | Typically less expensive. | More expensive due to the solid metal core and precision manufacturing. |
First, let’s talk about construction.
Spiral wound gaskets are made by alternating layers of metal and soft filler materials like graphite or PTFE, wound in a spiral shape. As shown here.
On the other hand, Kammprofile gaskets have a solid metal core with precision grooves on both sides. These grooves hold the sealing material, usually graphite or PTFE. As you can see in the image.
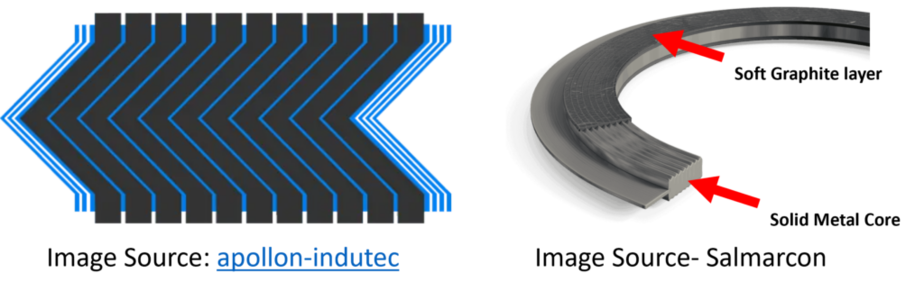
Second is the sealing mechanism.
The sealing mechanism is also different. Spiral wound gaskets rely on compressing the metal and filler layers, while Kammprofile gaskets use their grooves to deform the sealing material and create a tight seal.
So, incase of spiral wound both filler and metal strip get compression whereas only filler material gets compressed in kammprofile.
So, where would you use these gaskets? Spiral wound gaskets are flexible, making them perfect for almost all applications such as pipelines, vessels etc. where you need to handle medium pressure and thermal fluctuations. It also requires careful centering and controlled bolt tightening to avoid damage to the filler material.
Kammprofile gaskets, used in high-pressure, high-temperature applications where reliability is critical as it provides batter blowout resistance in high-integrity systems. It is easier to install and less sensitive to uneven bolt loads.
If you look at durability and cost, Spiral wound gaskets are usually single-use. The filler material often gets damaged during disassembly.
Kammprofile gaskets, on the other hand, can be reused if the core is intact. Just clean and recoat the sealing material.
Of course, this durability comes at a cost—Kammprofile gaskets are more expensive than spiral wound ones.
I hope you understand the differances.
Gasket Quiz – Test yourself, Take This Quiz