There are various Pipe Fittings Manufacturing Processes that are used to manufacture Elbow, Tee, Reducers, and other pipe fittings.
Fittings are manufactured from a Seamless Pipe and from Welded Pipe with filler material (ERW & EFW pipes cannot be used to manufacture fittings). large diameter fittings are manufactured from plates.
To manufacture wrought fitting various methods are used; these are the different types of Hot and cold forming processes.
- These methods are
- Hot forming or Extrusion Method
- Hydraulic Bulge method – Cold forming
- UO or Single weld seam Method
- Monaka or Double weld seam Method
- Deep Drawing Method for caps
- Flare Method for Stub ends
ELBOWS Manufacturing Process:
Mandrel method (Hot Forming)
- One of the most common Pipe Fittings Manufacturing process for manufacturing Elbows from the pipe is the mandrel method, a kind of hot forming method.
- In this method, the pipe is cut into pieces and pushed with the help of a hydraulic ram. An induction heating coil heats the pipe, and it is pushed over a die called a “mandrel,” which allows the pipe to expand and bend simultaneously.
- This method can be used to manufacture a wide range of the diameter of elbows.
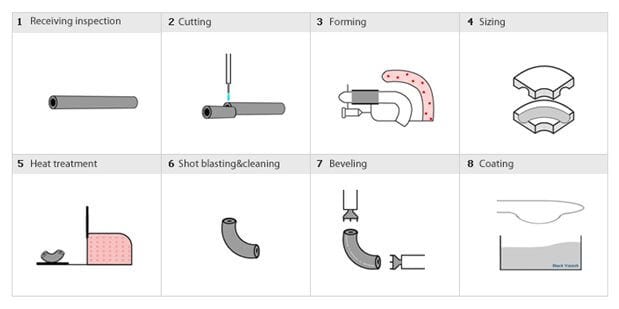
Extrusion Method
In the cold extrusion method, a pipe with the same diameter as a finished product is pushed through a die and formed into its desired shape. Usually applied to stainless steel small to medium sizes elbows.
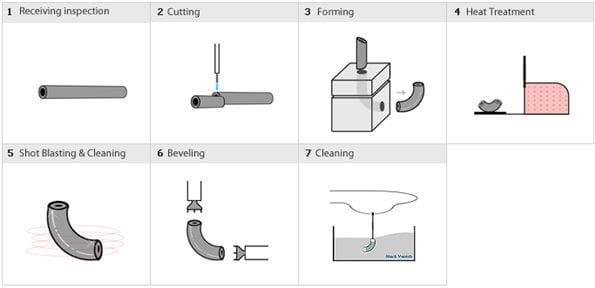
Pipe FIttings Quiz – Test yourself, Take This Quiz
Unlock New Skills with Our Best Selling Online Courses
UO Method
UO method is used to manufacture the medium size of elbow, tee, and reducers. The plate is cut out into a specially designed shape, it is formed first into a U-shape using a die and then into an O-shape or tubular form using another die; that is why this method is known as the UO method.
Once the fittings are tumbler shaped, they are welded from inside and outside of the closing seam. A cut plate is 1st from in U shape and then in O shape.
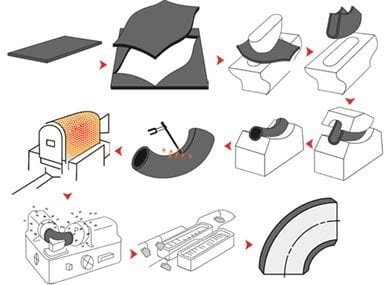
Image Source: Wermac.org
Hot Forming Method
In a Hot Forming Die Bending method, a Pipe is heated to forming temperature & formed in the die with the specific shape, this process may be repeated as needed to obtain the required shape, size, and wall thickness. Usually applied to thick-wall items that cannot be bent on a mandrel die. You can learn about elbows in this article.
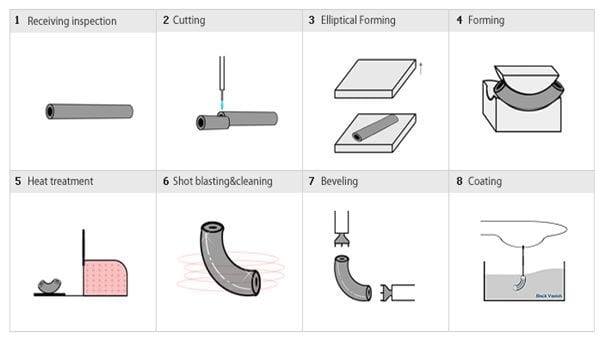
TEE Manufacturing Process
Hydraulic Bulge Method
The hydraulic Bulge method is used to manufacture Tee. Cut piece of Pipe is placed in hydraulic die and liquid is filled inside the pipe, Hydraulic pressure pushes out the branch, in the fixed opening in the die. This method gives a good surface finish. However, higher thickness Tee cannot be manufactured by this method.
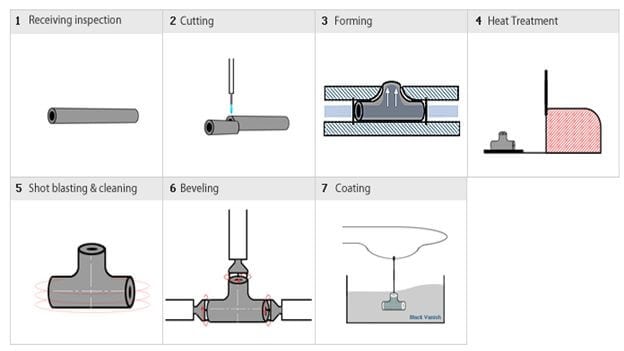
Unlock New Skills with Our Best Selling Online Courses
Hot Extrusion Method
Tee with large diameters, heavy wall thickness, and /or special material with challenging workability that cannot be manufactured using the hydraulic bulge method is manufactured using the hot Extrusion Method.
In the hot Extrusion Method, Normally Bigger diameter pipe is used than the finished product size, and the branch outlet is extruded from the pipe with the help of the extrusion tool. Other dimensions of the body and branch can also be adjusted by pressing the die if required.
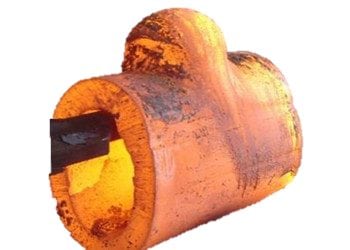
Reducer Manufacturing Process
Outer Die Method
The most common method for manufacturing Reducers is the Outer Die method. The pipe is cut and pressed into the outer die; compressing the one end of the pipe into a smaller size. This method is useful for manufacturing small to medium size of reducers.
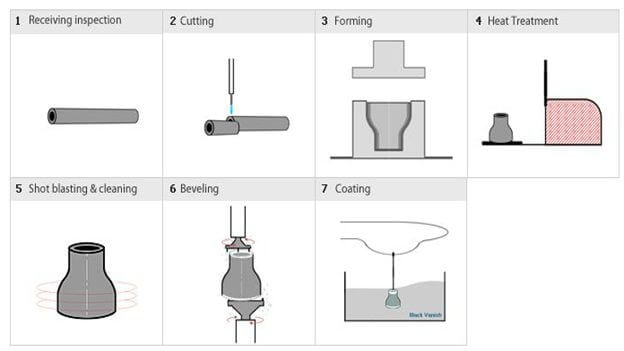
Cap Manufacturing Process
Deep Drawing Method
CAPS are manufactured by the Deep Drawing method. In this method, Plate is cut out in a circle and formed by a deep-drawing die.
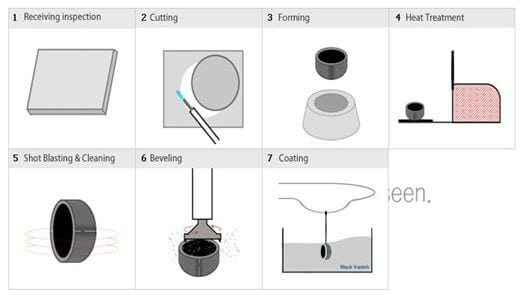
Stubend Manufacturing Process
Flaring Method
Stub Ends or Lap Joints Flange are manufactured by the flaring method. The pipe end is a flare or spared out from a flange face. Stub ends are also manufactured by forging, in which forge block is machined to the final dimension.
Fitting Heat Treatment
Hot finished pipe fittings do not require heat treatment; however, for Cold finished pipe fittings, Heat treatment is required as per applicable ASTM standards.
Common Heat Treatment for Fittings are listed below;
- Normalizing
- Quenching
- Tempering
- Solution Annealing
- Stress relieving
- And Combination of above
I have only covered well known Pipe Fittings Manufacturing Process here. There are many other methods that are used based on the requirements.
Image Source: TK Fittings
Are You Piping Components Master?