Pipe Fitting Inspection is carried out during the manufacturing of fittings. Various Inspections & Testing are carried out on pipe fitting to ensure the quality of the product.
Hydrotest for Pipe Fittings
- Hydrostatic Test Not required for pipe fittings unless specifically requested by the purchaser.
- Code mandates that fittings be able to withstand the pressure required by the applicable Piping Code.
- Most purchasers mandate that a hydro-tested pipe shall be used to manufacture fittings.
Proof Test
To qualify the design of the pipe fitting, the manufacturer performed various tests, including a burst test, to ensure that the design would meet all the standard & code requirements. In this test, a pipe & fittings are welded, and a dummy pipe spool is prepared.
This pipe spool is then pressurized to pre-define calculated burst test pressure. If the fittings withstand the test, all future products manufactured using that design will consider safe to use.
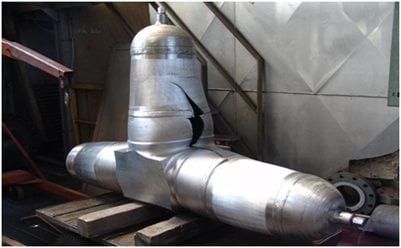
Lap joint stub ends are exempt from the proof test because they are used with flange assembly and design considering applicable pressure-temperature ratings.
Non-Destructive testing
Based on the type of fittings, any of the following Non-Destructive testings are performed on finished fittings to ensure the soundness of the product.
- Ultrasonic
- Radiography (Only for Weld)
- Magnetic particle test
- Liquid penetrant test
- And Positive Material Identification
Unlock New Skills with Our Best Selling Online Courses
Destructive Testing
Destructive Testings are performed to check the strength of the body and weld of the product.
- The proof test is also known as a Type Test or burst test.
- Tensile test
- Impact test / Charpy V-Notch Test
- Hardness test
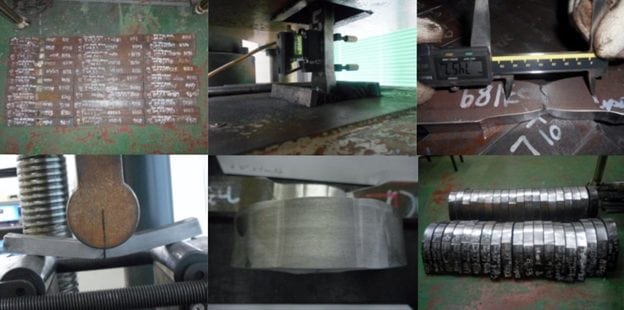
Pipe FIttings Quiz – Test yourself, Take This Quiz
Metallurgical Tests
Metallurgical Tests are performed on fittings body and weld to confirm standard requirements.
- Micro Analysis or Chemical Analysis of
- Raw material
- Product
- Weld
- Macro Analysis
- Weld
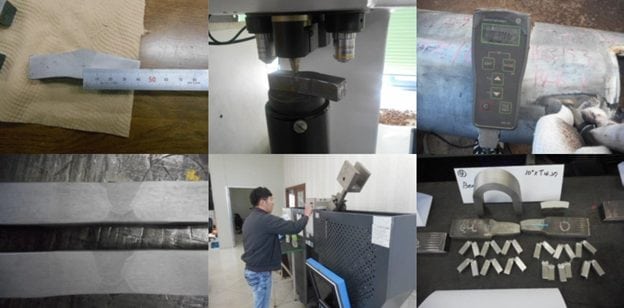
Special Tests
- Special tests are carried out on fittings to confirm their ability to withstand corrosive environments. These tests are
- IGC- Intergranular Corrosion Test(SS)
- Ferrite (SS)
- HIC- Hydrogen-induced Cracking
- And SSC- Sulfide Stress Corrosion Cracking
- Grain size (AS & SS) of material are checked to confirm microstructure
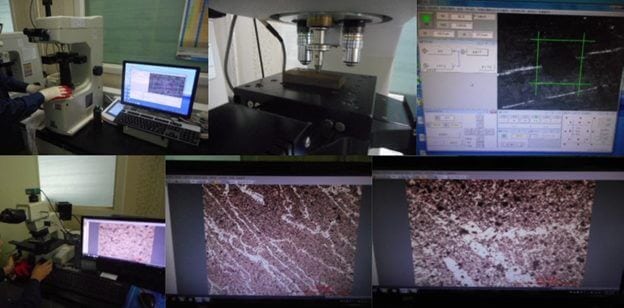
Visual Inspection of Pipe Fittings
Visual Inspection is conducted on fittings to check any surface imperfections. Both fittings body and weld are checked for any visible surface imperfections such as dents, die marks, porosity, undercuts, etc. Acceptance as per applicable standard.
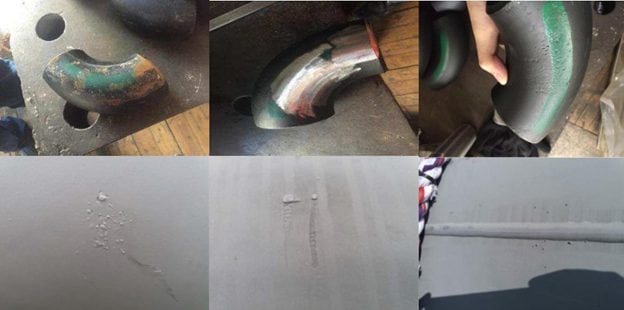
Pipe Fitting Marking
The following shall be marked on Fittings
- Manufacturer logo
- ASTM material code
- Material Grade
- Size, for tee size of branch & run pipe and for reducer size of both ends
- Thickness (Schedule No) for both the ends if they are connected to different thickness pipe
- Heat No
- Compliance – for standard fittings –WP, for Special fittings S58, S8, SPLD, etc.
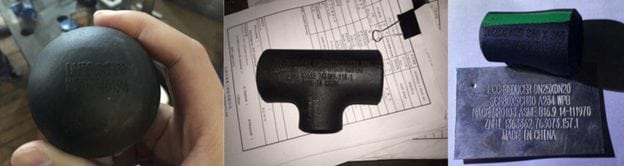
References:
- http://flange-fitting.com/
- TK Corporation http://www.tkbend.co.kr/
- Steel Tube India http://www.steeltubesindia.net/
Are You Piping Components Master?