Low Alloy Steel and High Alloy Steel are classifications of alloy steels based on the amount of alloying elements present.
Table of Contents
What is Alloy Steel?
When specific amounts of metallic and non-metallic elements are added to carbon steel, its properties are significantly altered. By adjusting the percentages of these alloying elements, we can enhance the characteristics of steel beyond those of plain carbon steel.
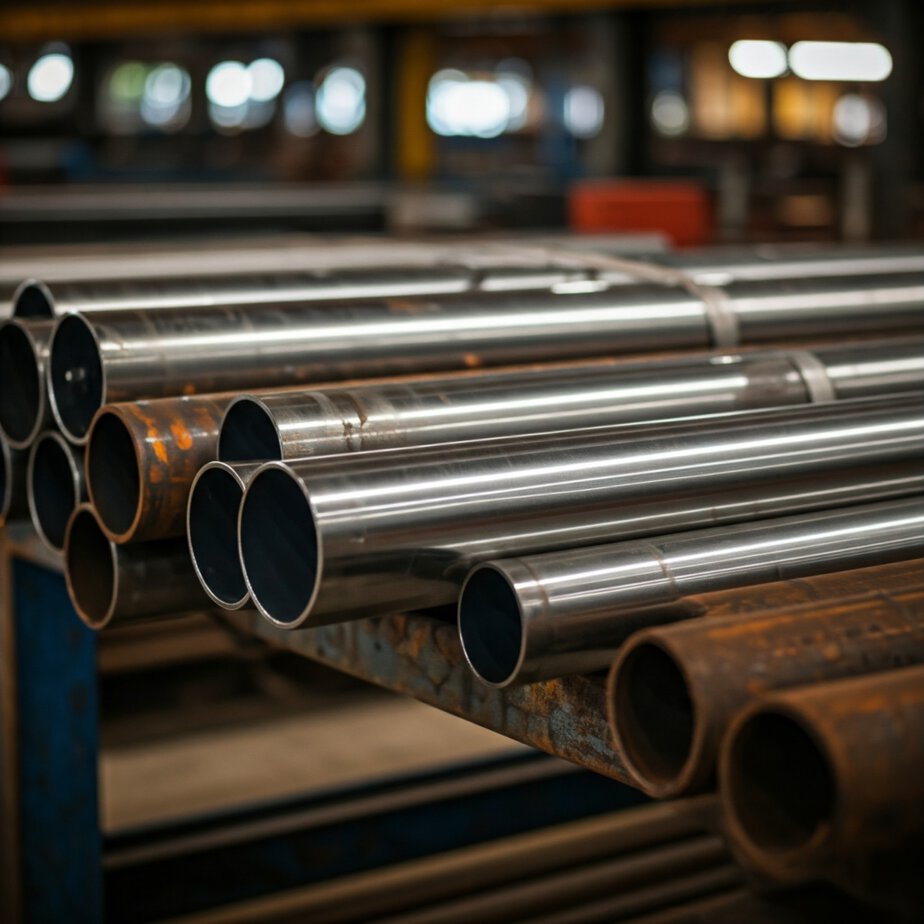
So, Alloy steels are steels that include additional elements, such as chromium, nickel, molybdenum, manganese, and vanadium, to improve their mechanical and chemical properties. Refer to the table given below for the key difference between Low Alloy Steel and High Alloy Steel.
Description | Low Alloy Steel | High Alloy Steel |
---|---|---|
Definition | Steel with total alloying elements less than 5-8% by weight. | Steel with total alloying elements exceeding 8% by weight. |
Common Elements | Chromium, molybdenum, nickel, manganese. | Chromium, nickel, molybdenum, vanadium. |
Properties | Good strength and toughness. | Excellent corrosion resistance. |
High strength and hardness, even at elevated temperatures. | High strength and hardness, even at elevated temperatures. | |
Moderate corrosion resistance. | Superior wear and abrasion resistance. | |
Enhanced wear resistance. | Retains properties in aggressive environments. | |
Suitable for tempering and quenching. | High durability. | |
Applications | Pressure: Pressure vessels, pipelines in oil and gas. | Corrosion Resistance: Chemical plants, food processing equipment, marine structures. |
High Temperature: Heater Tube and pipelines. | High Temperature: Turbines, boilers, and heat exchangers. | |
Wear: Heavy machinery parts, gears, and shafts. | Wear Resistance: Cutting tools, molds, and dies. | |
Structural: Bridges, buildings, and marine components. | Low Temperature: Cryogenic applications. | |
Automotive: Frames, axles, and suspension parts. | Aesthetic Applications: Architectural elements and kitchenware. | |
Examples | ASTM A335 grade P1, P5, P9, P11 | Stainless steels (304, 316, 410) |
Weldability | Good, but preheating and post-weld heat treatment may be required. | Good, often requires specialized techniques, purging and inerting. |
Corrosion Resistance | Moderate; can corrode in harsh environments unless protected. | High to very high; suitable for aggressive environments. |
Cost | Generally lower than high alloy steels. | Higher due to increased alloying elements and processing. |
What is Low Alloy Steel?
Definition: Steel with a total alloying element content typically less than 5% (but sometimes up to 8%) by weight.
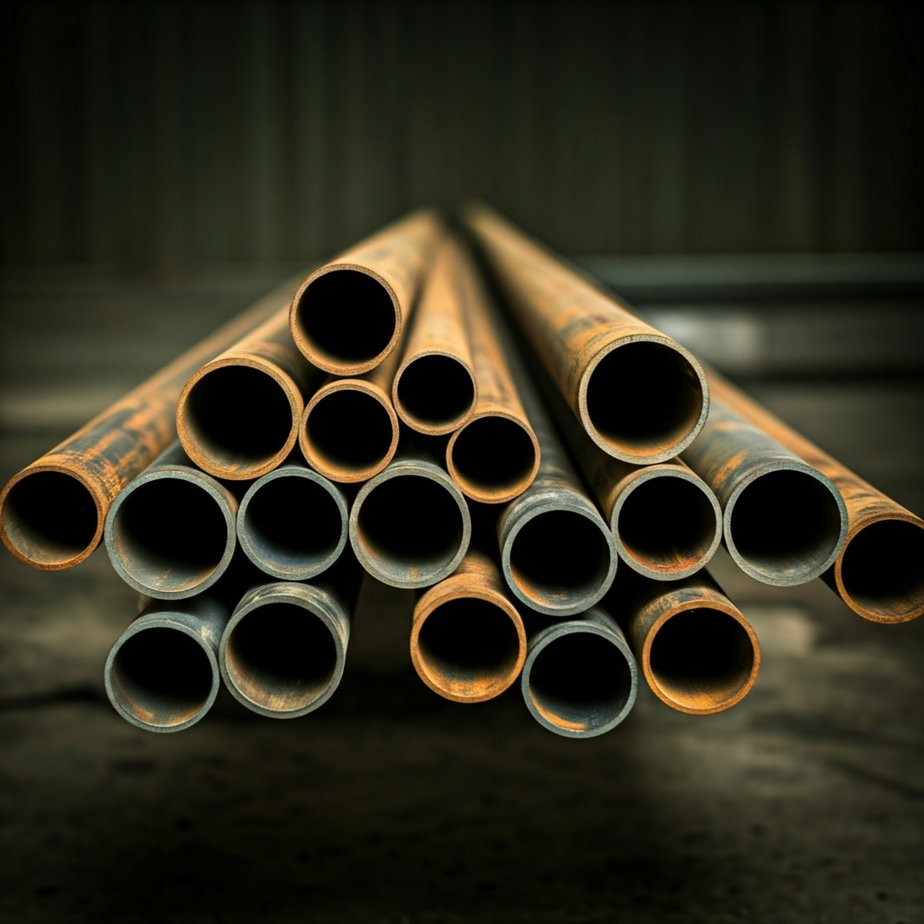
Properties:
- Higher strength compared to carbon steel.
- Improved resistance to corrosion, wear, and fatigue.
- Better toughness and hardenability.
Common Elements: Chromium, molybdenum, nickel, and manganese.
Applications:
- Structural components.
- Pressure vessels and piping.
- Automobiles and heavy machinery.
- Oil and gas pipelines.
Examples: ASTM A335 grade P1, P5, P9, P11
What is High Alloy Steel?
Definition: Steel with a total alloying element content exceeding 8% by weight.
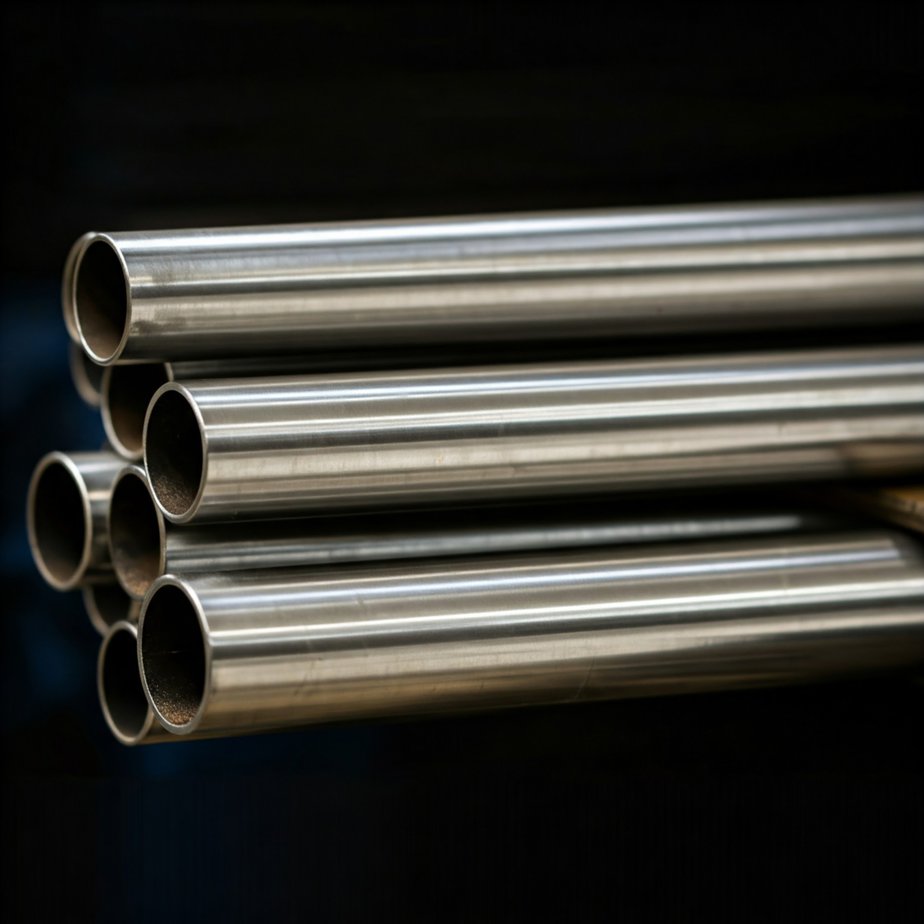
Properties:
- Exceptional resistance to corrosion and oxidation.
- Retains strength and hardness at high temperatures.
- High wear resistance and durability.
Common Elements: Chromium, nickel, molybdenum, and vanadium.
Applications:
- Stainless steels for corrosion-resistant environments (e.g., chemical plants, food processing).
- Tool steels for cutting and drilling.
- High-temperature applications (e.g., turbines and boilers).
Examples:
- Stainless Steels: 304, 316, 410.
In concussion, the main distinction is the amount of alloying elements:
- Low Alloy Steel: less than 5-8% alloy content.
- High Alloy Steel: more than 8% alloy content.
This classification impacts their mechanical properties, corrosion resistance, and suitability for various applications.
Piping Component Quiz – Test yourself, Take This Quiz