Here, I have listed the most commonly asked interview questions on the types of flanges used in process piping. As you know, piping flanges are key elements of a piping system and are used in various industries, such as oil and gas, petrochemical, manufacturing, and more.
These flanges connect pipes to valves or equipment, or to another pipe spool, and form a tight seal that prevents leaks and ensures efficient fluid flow within the system.
After reading these FAQs, you can take a quiz to check your understanding.
Common Questions on Types of Flanges Used in Piping
Q- What is a flange?
A- Flange is a type of piping component that is used to join pipe to pipe, or other piping components and equipment/ Flange consists of three components: metallic flange, which is welded or bolted with pipe or other equipment. The second is a gasket that seats between two flanges, and the third is the bolting material that keeps the connecting flanges together to create a secure and leak-proof connection.
Q- What is a flange used for?
A-Flanges are commonly used in piping systems, allowing for easy disassembly and maintenance of the system. They are also used in industrial equipment such as pumps, valves, and static equipment to connect them with piping systems.
Q- What are flange types?
A- Depending on the application and the requirements of the piping system or equipment, several types of flanges are used in piping. Such as weld neck, threaded, socket, etc.; refer to this article to learn about 10 main types.
Q-What are the 3 most common flange types?
A- Weldneck, Socket weld and Threaded are the most commonly used types of flanges in piping systems.
Q- What are the examples of flanges?
A- Weld neck, slip-on, socket weld, threaded, blind flange, and lap joint type flanges are some of the commonly used flanges.
Q- What is ASME B16.5?
A- ASME B16.5 is a standard for Pipe Flanges and Flanged Fittings for sizes NPS ½” to 24”. Don’t get confused between ASTM and ASME. These two are different standards. There is no ASTM B16.5.
Questions on Threaded Flanges
Q- What is a threaded flange?
A- A threaded flange is a type of flange that has threads on the inside bore, which allow it to be screwed onto a pipe or fitting.
Q- Where is threaded flange used?
A- Threaded flanges are commonly used in low-pressure applications where frequent disassembly may be required, such as plumbing, HVAC, and water treatment.
Questions on Socket-Weld Flanges
Q- What is a socket weld flange?
A- A socket weld flange is a type of flange with a socket or bore designed to fit over the end of a pipe and is then welded on the pipe, as shown in the image above.
Q- What is the socket flange used for?
A- The socket weld flange is commonly used in smaller size piping systems with low temperature and pressure applications.
Q- What is the difference between socket weld flange and slip on flange?
A- The main difference between a socket weld flange and a slip-on flange is the installation method. Socket weld flange require welding only on the outside of the joint as shown in the image above. Whereas, Slip on flange require welding on both the inside and outside of the joint as shown in the image below.
Q- What is the difference between a socket weld and a Buttweld flange (Weld neck flange)?
A- A socket weld flange and a butt weld flange are two different types of flanges that are used for different purposes.
A socket weld flange is a type of flange with a socket or bore designed to fit over the end of a pipe, and is then welded outside of the pipe with fillet-type welding. The socket weld flange is typically used in smaller size and Low-pressure temperature piping systems.
On the other hand, butt weld flange is a type of flange that is designed to be welded directly to the beveled end of the pipe, and it is used for high-pressure temperature applications in oil and gas, chemical processing, and power generation.
Unlock New Skills with Our Best Selling Online Courses
Questions on Slip-On Flanges
Q- What is slip on flanges?
A- A slip-on flange is a type of flange that is designed to slip over the end of a pipe or fitting and then be welded both inside and outside, as shown in the image above. Slip-on flanges have a slightly larger diameter than the pipe or fitting to which they are attached, allowing them to slip over the end of the pipe or fitting.
Q- What is the difference between slip on and weld neck flange?
A- The main difference between slip on and weld neck flange is how they are welded with the pipe. Slip on flange is fillet welded, whereas weld neck flange is butt welded with pipe. Slip-on flanges are commonly used in low-pressure applications where the welded joint is not subject to high stresses. Weld neck flanges are commonly used in high-pressure and high-temperature applications, where the joint is subject to high stresses.
Questions on Lap Joint Flanges
Q- What is lap joint flange?
A- A lap joint flange comprises two main parts: a stub end and a loose backing flange. The stub end is welded directly to the pipe, while the backing flange slides over the pipe and is not attached to it. The backing flange can be made of a different material than the stub end, and is often made of lower cost carbon steel.
Lap joint flanges are particularly useful in situations where the piping system needs to be frequently dismantled and reassembled. This is because the backing flange can be easily removed and reattached without removing the entire flange assembly. It is also used in piping systems where space is limited and a compact flange design is required.
Q- What is the difference between lap joint flange and slip on flange?
A- Lap flange consists of two parts: stub end and backing flange. In a lap joint flange, stub end is directly welded to the pipe by butt welding, while a slip-on flange is welded on the pipe by a fillet weld from inside and outside.
Q- What are two advantages of a lap joint flange?
A- The main two advantages of using a lap joint flange are listed below.
- Easy disassembly and maintenance: One advantage of lap joint flanges is that they are easy to dismantle and reassemble when maintenance or fast joining is required. The loose backing flange can be easily aligned with another flange, allowing the piping system to be easily disassembled and reassembled.
- Flexibility in material selection: Another advantage of lap joint flanges is that they allow for flexibility in material selection. The stub end can be made from a different material than the backing flange, which can be beneficial in situations where the material properties of the two components need to be different. For example, a stub end can be made of a corrosion-resistant material, with the backing flange made from a cheaper material, as it will never come in contact with a fluid.
Questions on Weld Neck Flanges
Q- What is the purpose of a weld neck flange?
A- The purpose of a weld neck flange is to provide a strong and secure connection between two joints (Pipe to pipe or pipes to valve, equipment, etc.). It has a long tapered neck (which is called a hub) that is welded that provides a smooth transition of the flow. Weld neck flanges are commonly used in high-pressure and high-temperature applications.
Q- What is the standard weld neck flange?
A- Flanges manufactured following the standards such as ASME B16.5, ASME B16.47, DIN, or other similar are called standard weld neck flanges.
Q – What are the parts of a weld neck flange?
A – Weld neck flange typically consists of three main parts:
- Flange body: This is the main part of the flange that connects to other flanges. It has a circular shape with bolt holes around the perimeter for attaching the flange.
- Tapered neck or hub: This flange portion is welded to the piping components or equipment. The tapered neck or hub extends from the flange body and gradually narrows down to the diameter of the pipe.
- Flange face: This is the surface of the flange that comes into contact with the gasket. Depending on the requirements, the flange face may be raised, RTJ, or flat.
Q- What are the different types of weld flanges?
A – Depending on the flange face, it can be a flat face, raised face, or RTJ type. Refer to the Flange Face section for more information.
Questions on Blind Flanges
Q-What is a blind flange?
A- Blind flange is a type of flange that is used to close off the end of a pipe or vessel. It is called a “blind” flange because it has no opening for fluid or gas to flow.
Q- Why use a blind flange?
A- Blind flanges are commonly used in piping systems where future connections may be needed or where the end of the line needs to be sealed off. They are also used in equipment to close off nozzle openings when not in use.
Q- How many types of blind flanges are there?
A- Blind Flabges are available in mainly three face types. Flat face, raised face, or RTJ type.
Q- What is the difference between a Blind flange and a Blank flange or Blind?
A- The terms “blind flange” and “blank flange” are sometimes used interchangeably, but they can refer to different types of flanges depending on the cont
As said earlier, a blind flange is a type of flange that is used to close off the end of a pipe or vessel nozzle. On the other hand, a blank (or it is called a blank flange by some) is used to isolate part of the piping system for short-term maintenance activities. Refer to the image given here for easy understanding.
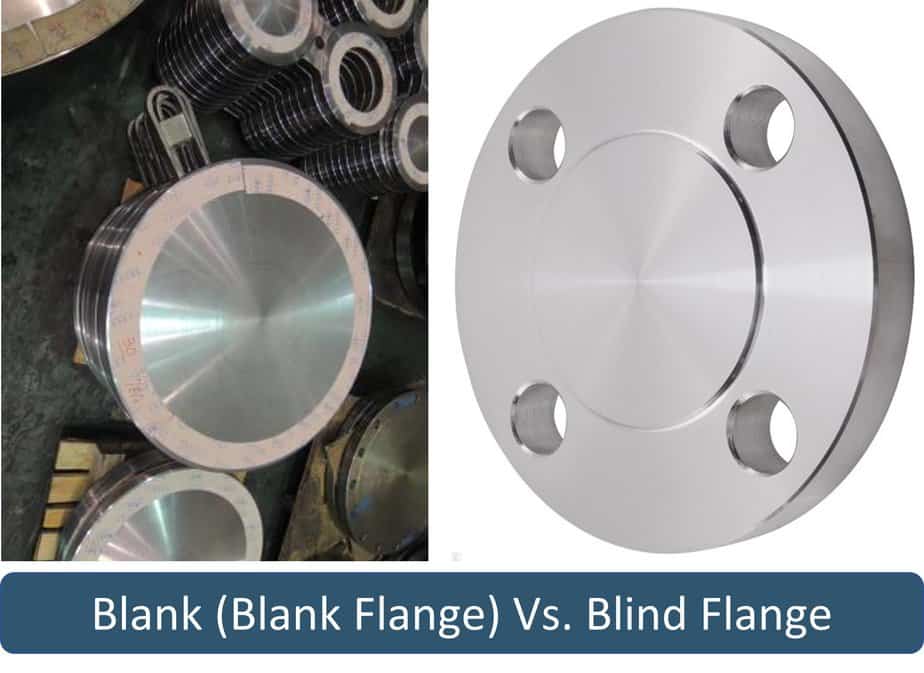
Question on Reducing Flange
Q- What is reducing flange?
A- Reducing flange is a type of flange that is designed to connect pipes or fittings of different sizes. It is similar in design to a regular flange but has a smaller diameter on connecting end, as shown in the image above.
Questions on Flange Faces Tyeps
Q- What is the difference between RF and FF?
A- RF is raised face, and FF is Flate Face. The main difference between RF and FF flanges is the shape of the sealing surface, as shown in the image below. RF flanges have a raised face, while FF flanges have a flat face.
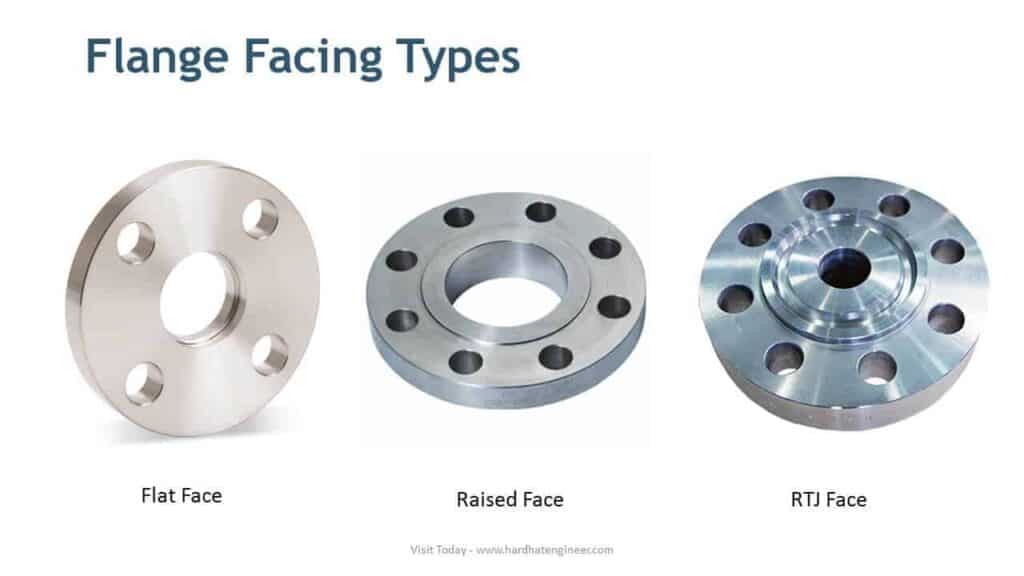
Q- What does RF and FF mean in flange?
A- RF means “Raised Face” and FF means “Flat Face”
Q-Can you mate / connect RF and FF flanges?
A- No, it is not good practice to connect RF and FF flanges.
Q-What is difference between RF and RTJ flanges?
A- RF and RTJ are two different types of flange faces, as shown in the image above. RTJ flange has a grove on the face in which metallic ring gasket seats.
Q-What does RTJ flange stand for?
A- RTJ stands for Ring Type Joint Gasket flange.
Quiz to Test Your Knowledge
Flange and Olet Quiz – Test yourself, Take This Quiz